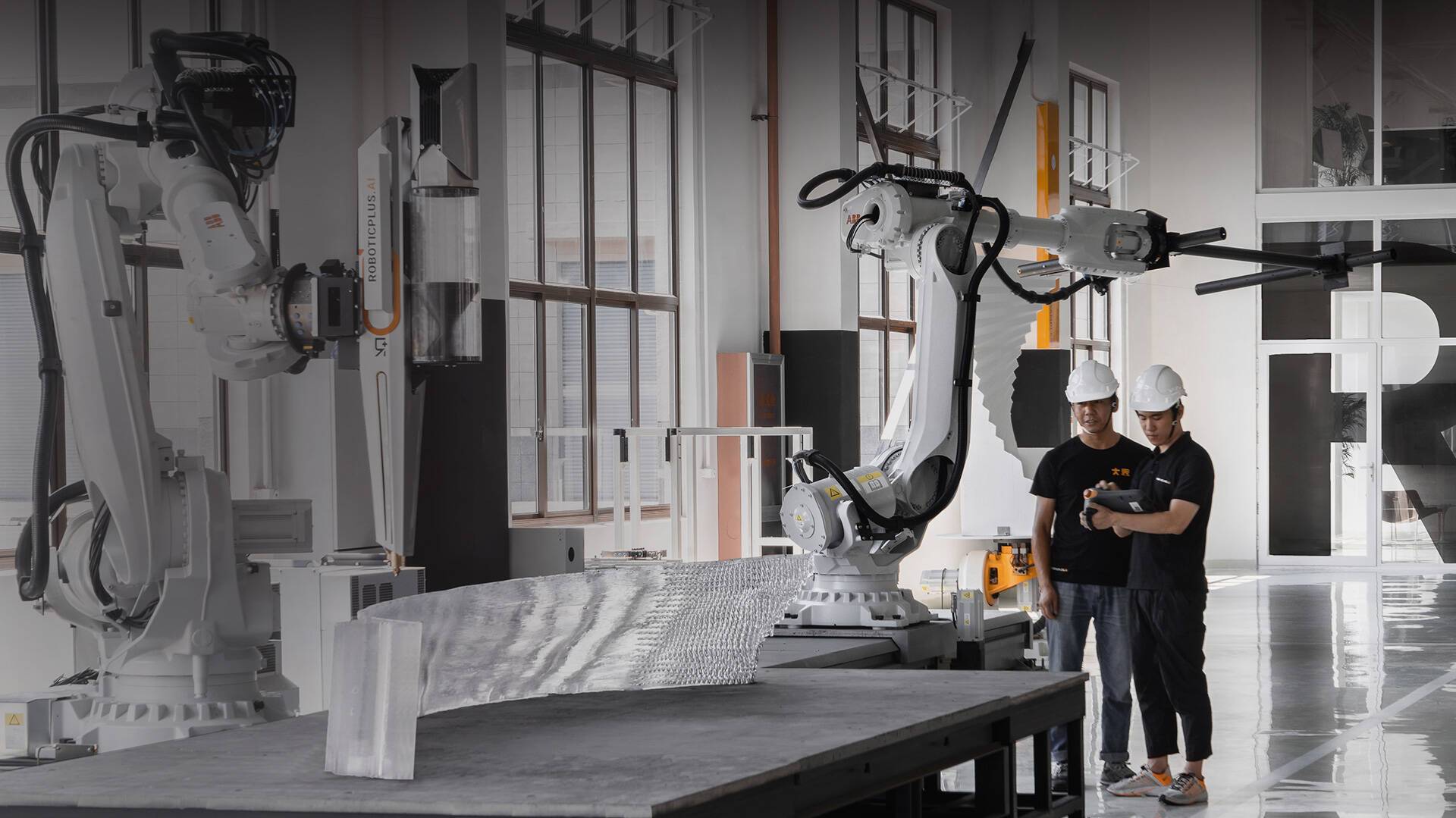
News
cutting-edge technology
Jiangnan Shipyard, a flagship of China Shipbuilding Group, boasts a rich legacy dating back to 1865. Renowned globally, it's a pioneer in military shipbuilding, with a track record of 'China's first' achievements.
As a digitalization benchmark, Jiangnan Shipyard has secured numerous orders for cutting-edge vessels, notably ultra-large dual-fuel-powered container ships and VLGCs. With VLGCs being the pinnacle of high-tech, high-value ship types, Jiangnan Shipyard's relentless pursuit of innovation has cemented its global market dominance.
To further its legacy of disrupting traditional manufacturing, Jiangnan Shipyard partners with RoboticPlus.AI to intelligently transform its profile cutting production line. This collaboration aims to unlock production capacity, catalyzing the shipbuilding industry's digital evolution.
RobimCutProfile 3D Cutting Solution
Autonomous, stable, and user-friendly, this solution revolutionizes profile cutting—a crucial technology in ship hull engineering. Featuring self-developed software and intelligent algorithms, it offers model data analysis, path planning, process simulation, and an expansive library of macros. Adaptable to diverse marine profile specifications, it enhances quality, efficiency, and manufacturing timelines for Jiangnan Shipyard.
We tailor our development to frontline production needs, crafting independent, flexible, and customizable intelligent software. Covering cutting process design, production execution, equipment maintenance, and capacity statistics, our operation is streamlined and fully automated with a single key.
We support GEN file output from TRIBON, AM, Catia, SPD, and other design software, offering over 100 macro libraries and unlimited expansion. Integrated with upper software systems, we support OPCUA, databases, Web Service/Web API communication methods, and custom development.
Equipped with advanced software and industrial-grade equipment, including a six-axis industrial robot, plasma cutting system, point laser sensor, servo pushing trolley, and high-precision encoder positioning device, we achieve full-process automation from loading to discharging.
Our mature process algorithm library ensures cutting accuracy up to ±1mm, covering a plate thickness range of 4-68mm. We employ heuristic algorithms based on Lagrangian relaxation theory for nesting, maximizing material utilization and achieving nesting times of less than 0.2 seconds.