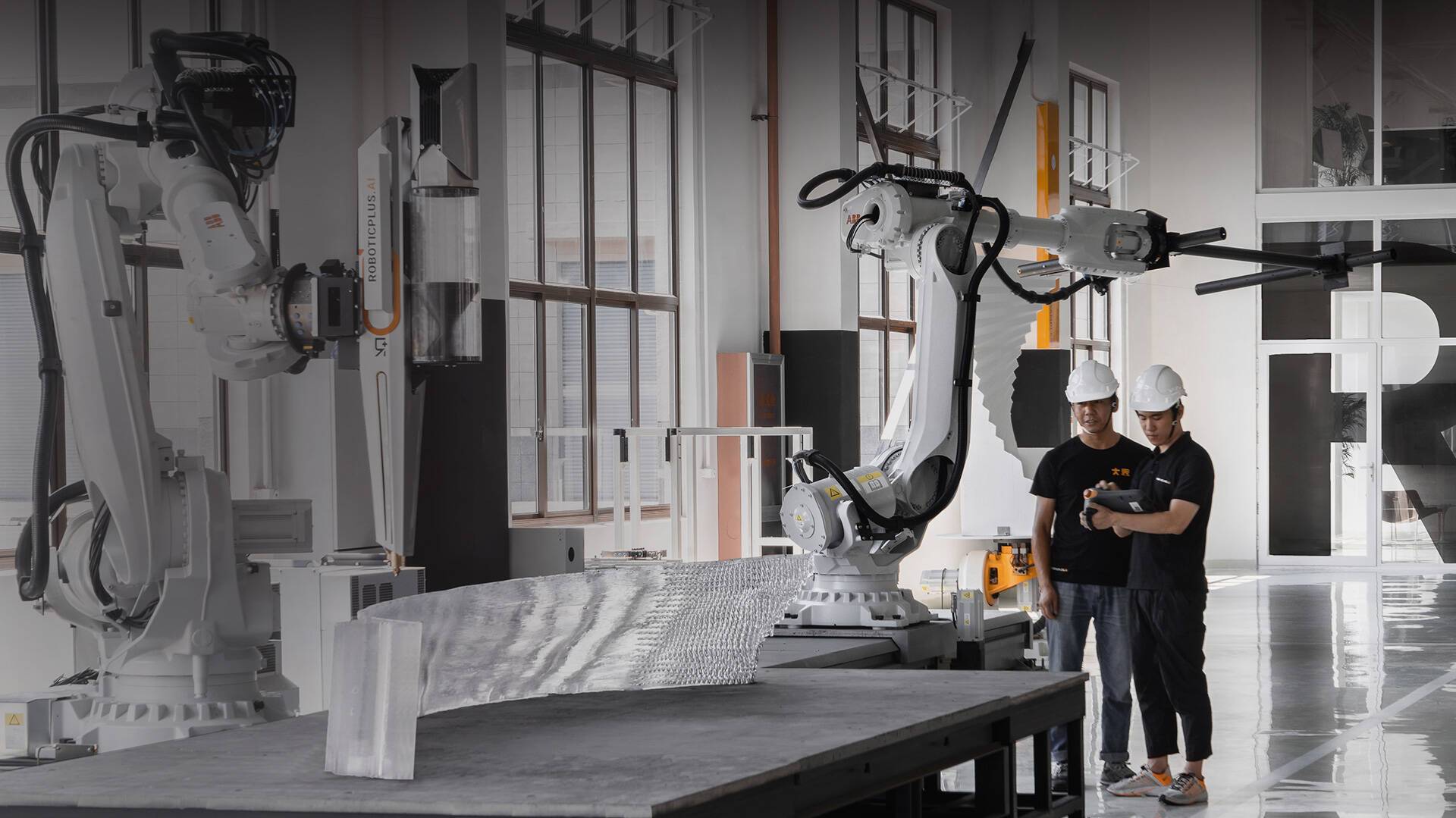
News
cutting-edge technology
Shanxi Coal Mining Machinery Manufacturing Co., Ltd., a prominent player in China's coal machinery industry, specializes in producing scraper conveyors and belt conveyors vital for underground coal transportation.
In an era emphasizing digitalization, intelligence, and green transformation, they've partnered with us to sustain their competitiveness and industry stature.
To address this, we've tailored a specialized beveling production line for Shanxi Coal Mining Machinery, markedly enhancing their production efficiency and quality.
Advantages:
1. The solution is a groundbreaking industry first, merging truss automatic loading and unloading with two six-axis robotic arms for collaborative cutting. It also incorporates flexible grinding tools for all types of bevel angles. This integration achieves a fully automated production process for center bottom plate workpieces.
2. Our solutions use RobimCut software and intelligent algorithms for easy data interfacing, automatic bevel parameter setup, and one-click robot program creation. The software is tailored to real production needs and doesn't require programming, making it user-friendly.
3,We use our vision algorithms and multi-sensor fusion technology to ensure precise workpiece positioning and machining accuracy. Additionally, our free path planning algorithms enable smooth robot operation without collision or interference, effortlessly adjusting to the field environment.
It calculates the center of gravity to securely grip workpieces, enhancing efficiency with quick handling and precise visual recognition.
It autonomously adjusts processing paths, schedules work beats, and controls speed and depth, resulting in an 80% efficiency increase compared to manual cutting.
4,It features an open port and seamlessly integrates with upstream MES systems and AGVs, enabling unmanned automatic material handling in the production line. This integration brings substantial economic benefits to the enterprise.